Ayalytical - Visaya เป็นผู้ผลิตเครื่องมือทดสอบทางด้านปิโตรเลียมรายใหม่ ที่พัฒนาเครื่องมือด้วย Digital Image Analyzer เทคโนโลยีใหม่ล่าสุด เพื่อรองรับการทดสอบตัวอย่างน้ำมันปิโตรเลียม น้ำมันเชื้อเพลิง น้ำมันเครื่องบิน น้ำมันหล่อลื่น สารเคมี และตัวทำละลายไฮโดรคาร์บอน เช่น เครื่องทดสอบค่าการกัดกร่อนทองแดง (Copper Corrosion - CuDDI) เครื่องทดสอบค่าการกัดกร่อนเงิน (Silver Corrosion - AgDDI) เครื่องทดสอบค่าการกัดกร่อนเหล็ก (Iron / Ferrous Corrosion - FeDDI) เครื่องทดสอบการเกิดฟองของน้ำมันหล่อลื่น (Foam Tester - FoamDDI) และเครื่องสอบเทียบค่า Permeability & Pore Size ของหัวเป่าฟอง (Diffusor Stone – StoneDDI นอกจากนี้ยังมีเครื่องทดสอบน้ำมันรายการอื่นๆ ที่จำหน่ายในเครื่องหมายการค้า“Lawler” ทุกชนิด
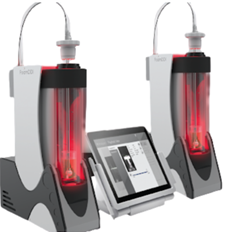
FoamDDI – Foam Digital Detection Imaging / เครื่องทดสอบการเกิดฟองของน้ำมันหล่อลื่น
BS 2000 Part 156, ASTM D892, ASTM D6082, FTM 791-3211, IP 146, ISO 6247
Full automation and Elimination of User Bias.
Contamination in the form of air, which can be foam or entrained air bubbles creates adverse effects in machinery and lubricants. Issues such as incomplete oil films, low oil pressures, accelerated oil degradation, and additive depletion are all symptoms of high foam tendency, which can produce metal wear, inadequate lubrication, cavitation in pumping, and mechanical failures. Standard Test Method ASTM D892 was really developed for lubrication testing and to determine the foaming characteristics of lubricant oils, by empirically rating their foaming tendency and stability. Standard Test Method ASTM D892 was developed to determine a lubricant’s ability to resist foam formation and dissipate foam creation. However, measuring foam heights is a challenge, as it relies on the human eye” to measure foam heights which creates a significant user resulting in human errors, bias, and poor repeatability and reproducibility. The FOAM Digital Detection Imaging (FoamDDI) accurately controls the airflow, temperature, and sequence, which is then augmented using a unique VISION algorithm to accurately determine the height of station and dynamic foam heights, while greatly improving the precision and accuracy.
Principle:
The all-new FoamDDI eliminates the need for sample manipulation and critical timing involved with regular foam detector methods. Using a patent-pending heating and cooling system with a vision algorithm and lubrication testing automation the FoamDDI, records, calculates, and displays accurate results with little to no operation bias. Determinations come from this foam detector in minutes!
- Using a high-resolution camera with state-of-the-art optics for lubrication testing, FoamDDI quickly brings a sample in the inserted cylinder to test temperature.
- After a soaking time, the foam detector and analyzer start air for FOAM production.
- Air Flow is controlled using Mass Air Flow Controllers (MFC)
- At the 5 min. mark, an LED light source is activated.
- VISION algorithm is activated and begins analyzes
- The complete sequence is recorded and analyzed.
- Test is completed or next sequence can automatically be continued if desired.

StoneDDI Stone Calibrator / เครื่องสอบเทียบค่า Permeability & Pore Size ของหัวเป่าฟอง
ASTM D892, ASTM D6082, FTM 791-3211, ISO 6247
Unbiased and reliable digital detection experience.
Performing foam stability and foaming tendencies of lubricant oils involves a tightly controlled flow of gas — typically air — being dispersed into a measured volume of the test liquid at predetermined conditions of time, air flows and temperatures. This is in accordance with standardized methods such as ASTM D892, D6082 and IP 146. The creation of foam can be associated with the nature of the oil in question and the efficiency in which the diffuser funnels air into the formulations being tested. A faulty diffuser impacts the quality of the analysis, therefore impacting the overall performance of the tests.
The determination of the foaming characteristics of lubricating oils at 24°C, 93.5°C and 150 °C, empirically rate the foaming tendency and the stability of the foam that might be formed in normal operations. The system is also capable of performing this at any temperature or conditions with equal ease. In both methods, FoamDDI eliminates any confusion that may arise when interpreting the procedure results, and guarantees compliance with test temperature requirements and exact definitions of kinetic and static foam performing the measurement at the correct times. These test methods require that the condition of the diffuser used has pore sizes and permeabilities. Calibration of diffusers to verify maximum pore size and permeability have been found to be critical factors for the tests. It is recommended that these diffusers be calibrated when new and periodically checked after each test.
The Stone
Digital Detection Imaging Apparatus (StoneDDI) easily provides unbiased
and reliable measurements of pore size distribution and flow rates of plastic,
ceramic, and metallic diffusers of different shapes and dimensions. StoneDDI is
the ultimate system for sample conditioning and testing. It is equipped with a
high-resolution CCD camera and reader unit that possesses state-of-the-art
optics. Together with the VISAYA FoamDDI algorithm, StoneDDI accurately
determines pore diameters and size distribution to unambiguously and
reproducibly calibrate them. For pore size verification, StoneDDI directs air
to the diffuser that is immersed in water in a glass measuring cylinder. The
high precision and accuracy of the calibration is guaranteed by the precise
control of air flows and procedural steps, adhering to the standard methods,
with minimal operator manipulation. This eliminates the critical timing
involved in the manual assessment and characterizes the calibrations by high
repeatability and reproducibility. The automatic system produces simultaneously
plots, pictures and videos allowing to visually and integrally characterize your
analyzers. The calibrator automatically measures the
pressure in Pa and converts it in mm H2O. The diameter is calculated by the
equation D = 8930/(PmmH2O-80) for metallic diffusers utilizing isopropanol as
the diffuser medium. The permeability is considered to be equal to the flow
rate measured at 2.45 kPa of pressure. The flow meter
calibration can be visually expressed as the reading in mm vs. the flows
measured at center of flow. Automated diffuser stone
calibrator for use with FoamDDI.
Used for certification of pore and permeability as required in ASTM D892 &
D6082.
Must be ordered and used with FoamDDI.
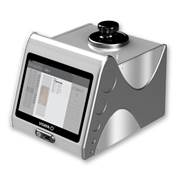
AgDDI – Silver Digital Detection Imaging / เครื่องทดสอบค่าการกัดกร่อนเงิน
ASTM D4814, ASTM D7671, IP 611
From qualified practitioner to quintessential professional, designed with the end user in mind.
Sensors in modern automotive fuel systems often use silver or silver alloys, which are susceptible to corrosion from sulfur in gasoline. In the past decade, refiners have shifted to producing lower-sulfur gasoline, but the process requires more severe hydro-treating that destroys naturally occurring compounds that give some protection against sulfur-based corrosion. Ensuring that fuel stays within acceptable limits requires constant and accurate corrosion testing equipment. Unfortunately, modern silver strip corrosion test methods rely heavily on user bias, as the operator must evaluate corrosivity by interpreting the color and tarnish level of a silver strip after it has been bathed in a fuel sample. AgDDI corrosion testing equipment, from Ayalytical Instruments (USA), uses a four-step automated vision algorithm and classification process to eliminate user bias. After evaluating the silver strip for corrosivity, the algorithm assigns the sample an integer between 0 and 4, with 0 being no corrosion at all and 4 showing significant blackening. AgDDI provides standardization to the current visual silver strip corrosion test as referred in ASTM D7671 and gasoline fuel specification ASTM D4814.
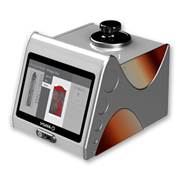
FeDDI – Iron/Rust Digital Detection Imaging / เครื่องทดสอบค่าการกัดกร่อนเหล็ก
JIS K2510, ASTM D665, ASTM D7548, IP 135, ISO 7120, NACE TM-01-72
A complete Automated Method to replace your difficult visual quantification.
Corrosion on steel pipelines and tanks can lead to destructive leaks that can cost millions to fix and cause irreversible environmental damage. As a result, industries spend billions each year on corrosion detection and to slow down the natural process of corrosion. The National Association of Corrosion Engineers (NACE) indicates that small amounts of water, air, and polar compounds are some of the biggest threats to petroleum pipeline corrosion. As such, NACE carefully monitors levels of corrosion by testing the interior of pipes for these substances. The NACE system of corrosion detection is dependent upon a manual rating process in which the operator must quantify small percentages of corrosion by visually inspecting a test specimen that has been bathed in a mixture of test fuel and distilled water. This method is highly susceptible to operator error. In addition, due to differences in visual acuity, results are not repeatable. FeDDI, from Ayalytical (USA), was designed to solve the difficulty rating of NACE TM0172 and D665 specimens accurately. It uses uses a four-step automated vision algorithm and classification process to eliminate user bias and provide repeatable results. After scanning a specimen’s entire surface area, corrosion coverage is quantified. FeDDI provides an complete automated method, which replaces the inherently difficult visual quantification referenced in NACE TM0172 and ASTM D665.
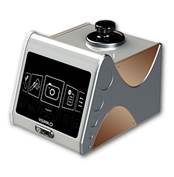
CuDDI – Copper Digital Detection Imaging / เครื่องทดสอบค่าการกัดกร่อนทองแดง
ASTM D130, ASTM D849, ASTM D1838, ASTM D4048, ASTM D4814, ASTM D7667, ASTM D7671, DIN 51 759, EN 2160, EN 6251, FTM 791-5325, IP 112, IP 154, IP 227, IP 411, IP 611, ISO 2160, ISO 22160
Identifying corrosivity levels with seamlessly integrated vision programming
Copper corrosivity has become a critical indicator of sulfur compounds present after the refining process. Prior to Copper Digital Detection Imaging (CuDDI), measuring corrosivity in petroleum presented a number of challenges. With no accurate standardized procedures in place, previous copper corrosion testing methods resulted in human error and bias due to manual visual assessments. CuDDI’s exclusive, patent pending copper corrosion test design takes the guesswork out of copper corrosion detection. Adhering to ASTM D130 and D1838, CuDDI precisely identifies corrosivity levels and eliminates operator bias through a 4-step automated vision algorithm and classification process. Its unique vision algorithm and light box records, calculates and displays accurate corrosivity ratings in a matter of seconds. CuDDI’s simplified, breakthrough procedure provides improved ratings, corrosion testing methods and sample handling over current tests. A high-resolution camera with sophisticated optics provides higher precision machining and motors for the rotation of the copper strip. Using a corrosion detection range of 1a through 4C, outcomes are digitally recorded and seamlessly integrate with LIMS software. The results are not only a groundbreaking improvement on current laboratory procedures; they are the new standard for copper detection.
The full CuDDI copper corrosion test method, features and specs can be viewed in the product brochure.
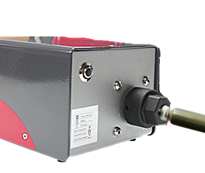
Automated NACE POLSHER / เครื่องขัดผิวตัวอย่างเหล็กสำหรับทดสอบค่าการกัดกร่อนเหล็ก
ASTM D665, ASTM D7548, NACE TM-01-72
Saving you time with automation.
The worlds Safest NACE Polisher, corrosion inhibition on the surface of the steel specimen exposed to conditions of water-saturated, warm air followed by condensing water.
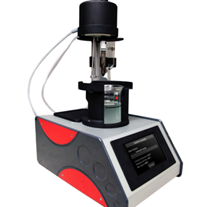
Automated NACE Apparatus (ANA) / เครื่องทดสอบค่าการกัดกร่อนเหล็ก
ASTM D665, ASTM D7548, NACE TM-01-72
Automate your sequencing process for your liquid hydrocarbon products!
The ANA (Automated NACE Apparatus) is a fully automated single position test apparatus to determine the corrosive properties of petroleum products and other liquid hydrocarbon products that are not water soluble for transport through a steel pipeline. The ANA saves you time by automating the sequencing process. This instrument features an embedded industrial grade programmable logic controller (PLC) with easy-to-use software, LCD display, and simple single button control for all functions. Sensors in modern automotive fuel systems often use iron or ferrous alloys, which are susceptible to corrosion from sulfur and other hetero compounds present in gasoline. In the past decade, refiners have shifted to producing lower-sulfur gasoline, but the process requires more severe hydro-treating that destroys naturally occurring compounds that give some protection against sulfur-based corrosion. Ensuring that fuel stays within acceptable corrosion limits requires constant and accurate testing.